Industrial helicoptered concrete floors
Dinamic Construct
Industrial helicoptered concrete floors
We like to keep things simple and keep our clients informed and up-to-date on the progress of their projects. We find ways to minimize waste and maximize our work ethic, all to increase the quality of our work and our staff. During the development of the project, our team will always be at hand to answer any question or concern you may have.
All works are carried out with military precision, by our specialized teams. Since there is no second chance when it comes to pouring and finishing industrial floors, this adds extra pressure and increased attention to every detail. The floor must be poured correctly the first time, and our experienced teams guarantee that your expectations will be met.
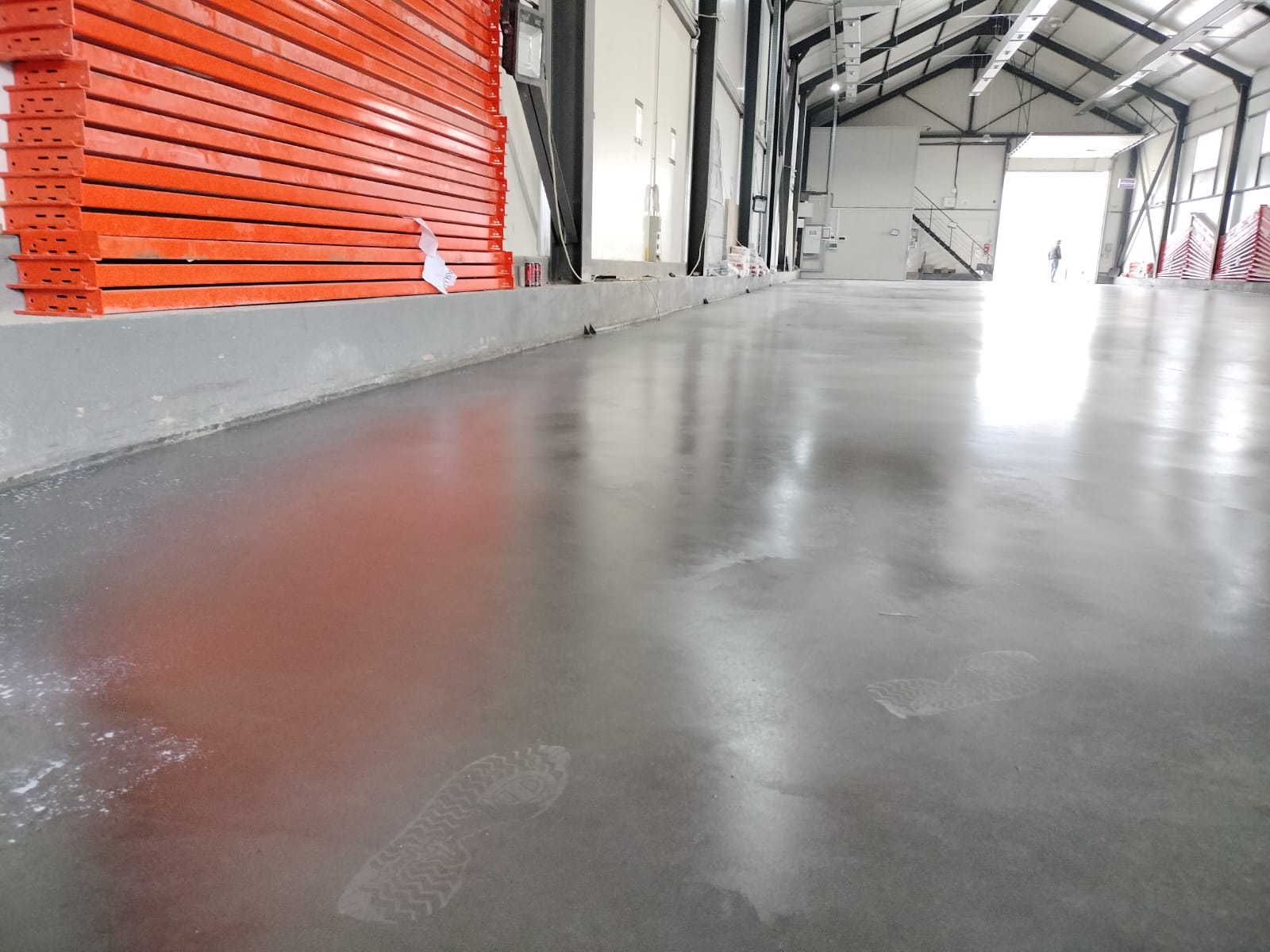
Dinamic Construct
Let a professional team with specialized tools and equipment do it
take care of your floor!

Dinamic Construct
Industrial helicoptered concrete floors
Every flooring project we receive goes through a rigorous planning process to ensure that your requirements are met. The accumulated knowledge and experience allow our clients to put their trust in the quality of the services offered.
br
Thanks to modern techniques and an experienced workforce, we are able to cast surfaces of up to 2,500m2 to the highest flatness standard.
Depending on the type of finish required and the way the surface is to be used, our operators can perform a variety of finishing techniques, such as:
Glossy finish – typical wear finish, used especially in warehouses and some shopping centers
Fine finish – cost-effective method for tiles that receive additional decorative finishes (epoxy resins, moschta, parquet or tiles).
Brushed finish – a textured finish to improve grip and slip resistance on roads, especially in winter.
Glossy finish – typical wear finish, used especially in warehouses and some shopping centers
Fine finish – cost-effective method for tiles that receive additional decorative finishes (epoxy resins, moschta, parquet or tiles).
Brushed finish – a textured finish to improve grip and slip resistance on roads, especially in winter.
Dinamic Construct
Industrial helicoptered concrete floors
If your flooring was not executed to a high standard, or was done by inexperienced workers, it can be very expensive to rectify it. There are several factors that you need to address regarding your industrial flooring:
Surface dust
Premature wear (durability)
Cracks in the depth of the concrete slab
Surface dust
Premature wear (durability)
Cracks in the depth of the concrete slab
To eliminate the risk of surface dust and premature wear, we apply a surface hardener (quartz) to the surface of the fresh concrete.
The floor hardener is a preliminary mixture consisting of cement, aggregate plasticizers and pigments, applied to the concrete surface during the concrete pouring process, or at the beginning of the mechanical chipping operation (helicopterization), improving both durability and abrasion resistance, and when necessary, it can include colored pigments to obtain various shades of color. It can also be used as a suppressor to reduce the number of visible fibers on a steel fiber reinforced flooring.


Dinamic Construct
Alpha type metal joints
The metal joints are lost formwork, used at the working joints of concrete floors, to prevent their grinding or chipping by forklifts or pallet trucks.
At the same time, these damaged joints, as they get worse, cause great losses to the owners of storage spaces, due to the rapid wear of the wheels of the forklifts or pallet trucks that cross them.
The metal joints allow the load to be transferred from one side of the joint to the other, creating a stable and durable floor, offering minimal maintenance to the warehouse owners.
The metal joints allow the load to be transferred from one side of the joint to the other, creating a stable and durable floor, offering minimal maintenance to the warehouse owners.
Dinamic Construct
Contraction joints
The cuts of the contraction joints are made to control the cracks due to the strengthening contractions in the concrete slab.
In an ideal world, the cuts should be made in a predetermined pattern, after the concrete has hardened and before any cracks appear.
In addition to the class of concrete used, the weather conditions play an important role when cutting the contraction joints must be started.
Cutting too early causes chipping and weakening of the joint, as the aggregate is pushed out of the concrete.
Cutting too late can lead to uncontrolled cracking due to strengthening contractions.
In hot weather it is even more difficult to establish the timing of cutting.
Ideally, cutting the joints should start as soon as the concrete stops grinding, after several test cuts have been made, at a depth between 1/4-1/3 of the plate thickness.
Cutting too early causes chipping and weakening of the joint, as the aggregate is pushed out of the concrete.
Cutting too late can lead to uncontrolled cracking due to strengthening contractions.
In hot weather it is even more difficult to establish the timing of cutting.
Ideally, cutting the joints should start as soon as the concrete stops grinding, after several test cuts have been made, at a depth between 1/4-1/3 of the plate thickness.


Dinamic Construct
Alpha type metal joints
In order to obtain maximum control of contractions, the tiles resulting from cutting the joints must have a square shape, with a maximum side of 6m.
The greater the number of joints, the less the contraction effort that each slab must bear.
br
Joints practiced too far apart can cause additional cracks in the middle of the slab.
br
Our engineers are happy to provide guidance on the layout of the contraction joints.
If you are thinking of transforming your industrial spaces and you are not sure where to start, why not give us a quick call? br Our friendly staff is always at hand to give you expert advice and can guide you on the best way to find the right solutions for your business.
If you are thinking of transforming your industrial spaces and you are not sure where to start, why not give us a quick call? br Our friendly staff is always at hand to give you expert advice and can guide you on the best way to find the right solutions for your business.